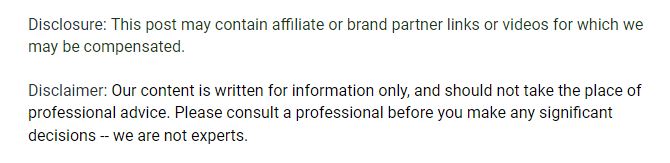

UPDATED 1/21/21
Air compressors change normal air into high pressurized and denser air for uses under three categories: industrial, professional, and consumer.
Air compressors are used in manufacturing, construction, engines, agriculture, spray painting, heating, ventilation, pressure washing, air conditioning, and the energy sector.
Things you need to know when purchasing air compressors
It might be your first time planning to buy an air compressor, and you are wondering how to select a compressor. Those who know how to run an air compressor should look out for the following things before buying it.
Check the horse pipe, cubic feet per minute, air pressure, tank sizes, duty cycle, moisture problems, and tank sizes. Confirm if the compressor is a single-stage or two-stage, is it a direct drive or belt drive, and lastly, check if it uses oil or functions oil-less.
Guidelines on using air compressors
It is advisable to be keen when using air compressors, especially heavy air compressor. Do you know how compressed air engine works? There several signs you ought to do before using a compressor. Plugin the compressor, check the oil levels, ensure you fill the air tank, check the air control valve and adjust it. Connect air hose, connect the pneumatic tool and finally drain moisture after use.
Compressed air systems are an integral part of 70% of all manufacturing plants in America. Compressed air is used for everything from cleaning to producing needed pressure for pneumatic drills and other tools. It makes sense then that a faulty compressed air distribution system can cost a factory both time and money. Having a source for repairing or replacing compressed air piping materials is an important part of any factory that depends on compressed air piping materials.
One of the ways that intake cooling air is lost is when the air is not properly cooled. For instance, when intaking cooler air, which is more dense, compressors use less energy to produce the needed pressure. For example, if 90 degree intake air is combined with cooler air from another source to 70 degrees, the 20 degree temperature drop will lower operating costs by as much as 3.8%. Even a small difference in the temperature can lead to beneficial savings or unfortunate expenses. Having a system of checks and balances that is able to constantly monitor the intake cooling air pressure is the first step toward saving energy costs and increasing productivity.
Like all constantly used pieces of machinery, air compressors require detailed and consistent service. Often, these routine maintenance checks are completed in house. Fixing, rather than simply making note of, problems keep air compressors and their various components working at their most efficient levels.
Compressed air system design has not changed much in the last few decades. These standard systems, in fact, can remain in operation for years if they are properly serviced and maintained. Any leaks, however, must be dealt with promptly if a manufacturer wants to continue operating at its highest levels. For instance, a compressed-air system leak of even an 1/8 inch diameter hole in a 100 psi system can cost a company more than $1,200 a year in wasted energy. the maintenance philosophy needs to be to immediately fix all sizeable leaks. Even if this means that a compressor unit has to be temporarily shut down, the interruption for repair is worth the extensive future energy that would be lost if the problem were not fixed.
You must be logged in to post a comment.